Ready for a new challenge, what about
the next big “Leak” issue. Only this time it
is international in scope and involves the building’s
piping system, leaking from the effects of corrosion.
Out of sight and out of mind, hidden behind
walls and in ceiling cavities, water pipes have been deteriorating
with few paying any attention to scope of the problem and
the potential cost to cure.
For those involved in the appraisal profession
it may be time to take a look behind those walls, so to
speak, and understand just what is happening to those water
lines. Consider the effects on building valuation and how
repairs can be made to mitigate direct damage and loss of
revenue.
In this article we will look at the causes
of corrosion in a piping system, traditional repair methods
and how a modern system of pipe restoration, not only repairs
the piping system while it is in the walls of the building
but stops the corrosion process from coming back. With pipe
restoration, no walls need to be torn out, no tile to be
removed, no mess, loss of room revenue is kept to a minimum
and typically a piping system can be restored in ½
the time with savings in the 30% to 60% range over the cost
of a conventional re-pipe.
Ready for a new challenge, what about the
next big “Leak” issue. Only this time it is
international in scope and involves the building’s
piping system, leaking from the effects of corrosion.
Out of sight and out of mind, hidden behind
walls and in ceiling cavities, water pipes have been deteriorating
with few paying any attention to scope of the problem and
the potential cost to cure.
For those involved in the appraisal profession
it may be time to take a look behind those walls, so to
speak, and understand just what is happening to those water
lines. Consider the effects on building valuation and how
repairs can be made to mitigate direct damage and loss of
revenue.
In this article we will look at the causes
of corrosion in a piping system, traditional repair methods
and how a modern system of pipe restoration, not only repairs
the piping system while it is in the walls of the building
but stops the corrosion process from coming back. With pipe
restoration, no walls need to be torn out, no tile to be
removed, no mess, loss of room revenue is kept to a minimum
and typically a piping system can be restored in ½
the time with savings in the 30% to 60% range over the cost
of a conventional re-pipe.
WHAT TO ASK AND WHAT TO LOOK FOR?
A good starting place is to get familiar with
the pH levels in your local water supply. A low pH will
indicate the water has an acidic nature which can be corrosive
to a piping system.
When on site, your inspection of the building’s
mechanical systems should include a look at the piping system.
Note the type of material the piping system is constructed
of. If copper, look for green stains in sinks or tubs. In
areas where the pipe is visible look for evidence of leaks
or repairs including sections of new pipe or the use of
gear clamps, which are used as a temporary stop gap measure
on pin hole leaks. Look for water stains on ceilings and
ask the question to the building manager about his experience
with leaks in the piping system.
If the piping system is constructed of galvanized
steel, again look for evidence of repairs or leaks but also
check the water pressure as you tour the building. Low water
pressure and changing water pressure usually indicates that
the pipes are encrusted and the water flow is being restricted.
As well as asking the building manager about leaks, repairs
and water pressure, ask about water pump replacement. Pumps
that work harder to deliver water through heavily encrusted
pipes usually wear out faster, another good indicator of
encrusted pipes.
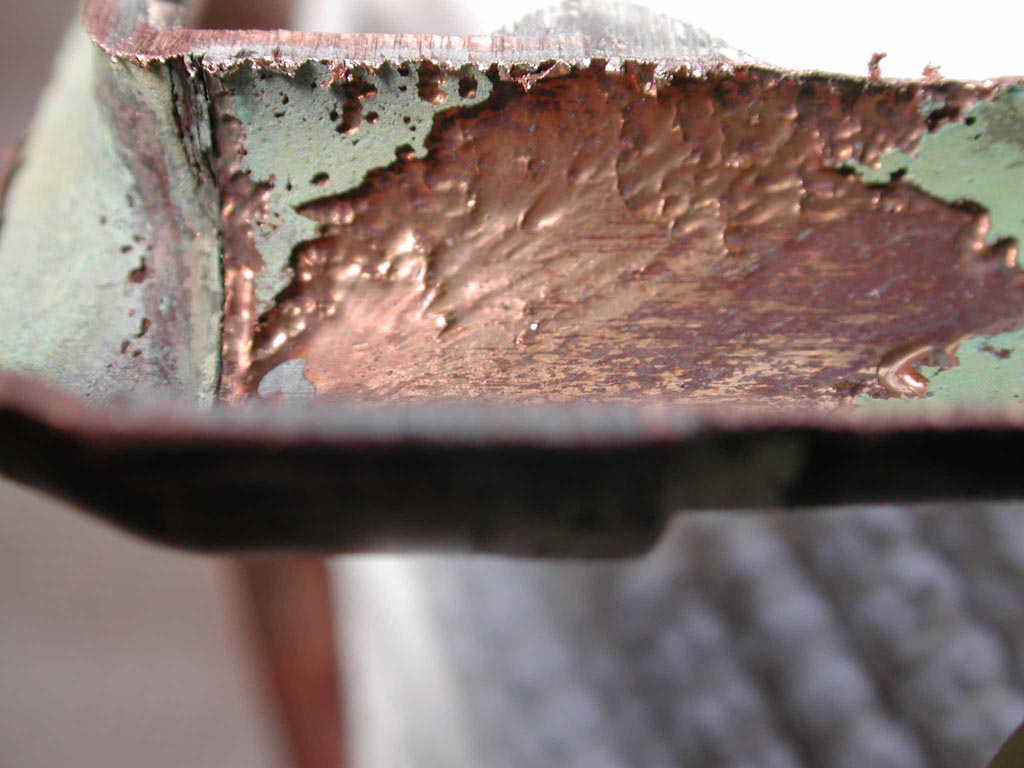
A good starting place is to get familiar with
the pH levels in your local water supply. A low pH will
indicate the water has an acidic nature which can be corrosive
to a piping system.
When on site, your inspection of the building’s
mechanical systems should include a look at the piping system.
Note the type of material the piping system is constructed
of. If copper, look for green stains in sinks or tubs. In
areas where the pipe is visible look for evidence of leaks
or repairs including sections of new pipe or the use of
gear clamps, which are used as a temporary stop gap measure
on pin hole leaks. Look for water stains on ceilings and
ask the question to the building manager about his experience
with leaks in the piping system.
If the piping system is constructed of galvanized
steel, again look for evidence of repairs or leaks but also
check the water pressure as you tour the building. Low water
pressure and changing water pressure usually indicates that
the pipes are encrusted and the water flow is being restricted.
As well as asking the building manager about leaks, repairs
and water pressure, ask about water pump replacement. Pumps
that work harder to deliver water through heavily encrusted
pipes usually wear out faster, another good indicator of
encrusted pipes.
|