BOILER
is a pressure vessel designed to transfer heat A(produced
by combustion) to a fluid. The definition has been expanded
to include transfer of heat from electrical resistance elements
to the fluid or by direct action of electrodes on the fluid.
In most boilers, the fluid is usually water in the form of
liquid or steam. If the fluid being heated is air, the heat
exchange device is called a furnace, not a boiler. The firebox,
or combustion chamber, of some
boilers is also called a furnace.
Excluding special and unusual fluids, materials, and methods,
a boiler is a cast-iron, steel, aluminum, or copper pressure
vessel heat exchanger designed to (1) burn fossil fuels
(or use electric current) and (2) transfer the released
heat to water (in water boilers) or to water and steam (in
steam boilers). Boiler heating surface is the area of fluid-backed
surface exposed to the products of combustion, or the fire-side
surface. Various codes and standards define allowable heat
transfer rates in terms of heating surface. Boiler designs
provide for connections to a piping system, which delivers
heated fluid to the point of use and returns the cooled
fluid to the boiler.
A boiler is a closed vessel that heats water
to a pre-set temperature and feeds it to a circulator, which
transfers the water to radiant heating units including some
or all of cast iron radiators, slim baseboard radiators,
under floor tubing or wall panels. Some boilers produce
steam for heating purposes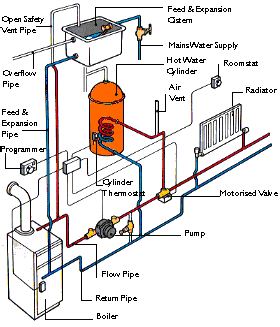
CLASSIFICATIONS
Boilers may be grouped into classes based on working pressure
and temperature, fuel used, material of construction, type
of draft
(natural or mechanical), and whether they are condensing
or non
condensing. They may also be classified according to shape
and
size, application (such as heating or process), and the
state of the
output medium (steam or water). Boiler classifications are
important to the specifying engineer because they affect
performance,
first cost, and space requirements. Excluding designed-to-order
boilers, significant class descriptions are given in boiler
catalogs or
are available from the boiler manufacturer. The following
basic
classifications may be helpful.
Working Pressure and Temperature
With few exceptions, boilers are constructed to meet ASME
Boiler and Pressure Vessel Code, Section IV (SCIV), Rules
for
Construction of Heating Boilers (low-pressure boilers),
or Section
I (SCI), Rules for Construction of Power Boilers (high-pressure
boilers).
Low-pressure boilers are constructed for maximum working
pressures of 15 psig steam and up to 160 psig hot water.
Hot water
boilers are limited to 250°F operating temperature.
Operating and
safety controls and relief valves, which limit temperature
and pressure, are ancillary devices required to protect
the boiler and prevent
operation beyond design limits.
High-pressure boilers are designed to operate above 15
psig
steam, or above 160 psig and/or 250°F for water boilers.
Similarly,
operating and safety controls and relief valves are required.
Hydronic and Steam
Heating Equipment and Systems.
Steam boilers are generally available in standard sizes
up to and
above 100,000 lb steam/h (60,000 to over 100,000,000 Btu/h),
many of which are used for space heating applications in
both new
and existing systems. On larger installations, they may
also provide
steam for auxiliary uses, such as hot water heat exchangers,
absorption cooling, laundry, and sterilizers. In addition,
many steam boilers provide steam at various temperatures
and pressures for a wide
variety of industrial processes.
Water boilers are generally available in standard sizes
from
35,000 to over 100,000,000 Btu/h, many of which are in the
low
pressure class and are used primarily for space heating
applications
in both new and existing systems. Some water boilers may
be
equipped with either internal or external heat exchangers
for domestic water service.
Every steam or water boiler is rated for a maximum working
pressure that is determined by the applicable boiler code
under
which it is constructed and tested. When installed, it also
must be
equipped at a minimum with operation and safety controls
and pressure/temperature-relief devices mandated by such
codes.
Fuel Used
Boilers may be designed to burn coal, wood, various grades
of fuel oil, waste oil, various types of fuel gas, or to
operate as electric boilers. A boiler designed for one specific
fuel type may not be convertible to another type of fuel.
Some boilers can be adapted to burn coal, oil, or gas. Several
designs accommodate firing oil or gas, and other designs
permit firing dual-fuel burning equipment. Accommodating
various fuel burning equipment is a fundamental concern
of boiler manufacturers, who can furnish details to a specifying
engineer. The manufacturer is responsible for performance
and rating according to the code or standard for the fuel
used
Construction Materials
Most noncondensing boilers are made with
cast iron sections or steel.
Some small boilers are made of copper or copper-clad steel.
Condensing boilers are typically made of stainless steel
or aluminum.
Cast-iron sectional boilers generally are designed according
to
ASME SCIV requirements and range in size from 35,000 to
13,975,000 Btu/h gross output. They are constructed of individually
cast sections, assembled into blocks (assemblies) of sections.
Push
or screw nipples, gaskets, and/or an external header join
the sections
pressure-tight and provide passages for the water, steam,
and products of combustion. The number of sections assembled
determines the boiler size and energy rating. Sections may
be vertical or horizontal, the vertical design being more
common
|