May 31, 1986
IPesticide Warehouse Fire
Canning, Nova Scotia
In the early morning hours of May 31, 1986, a fire broke
out at Maple Leaf Farm Supplies Limited pesticide warehouse
situated on Main Street, Canning, Nova Scotia. A large variety
and quantity of agricultural products including pesticides,
herbicides, fumigants, and fertilizers were stored in the
building along with seed grains, seed and table potatoes,
propane cylinders and miscellaneous farm machinery.
During firefighting operations, an estimated 1.2 million
litres of water was used; much of this contaminated water
migrated off site passing over adjacent residential properties,
into a farmer's pond and eventually finding its way into
the Habitant River via drainage ditches and storm drains.
Vegetation and large numbers of worms were killed in the
path of the water, and fish and invertebrates died in a
local farmer's pond as well as downstream in the Habitant
River. A trench was dug to intercept contaminated runoff
and wash water during the cleanup phase; however, this trench
was constructed after the bulk of fire fighting water had
left the site. Roughly 100,000 litres of water was treated
by a membrane filtration process known as reverse osmosis
to remove contaminants prior to discharge.Several hours
after the fire was discovered, municipal and local fire
and police officials began evacuating the village of Canning;
residents living closest to the fire site were not permitted
to return to their homes for six days. A multidisciplinary
emergency response and cleanup effort was immediately initiate
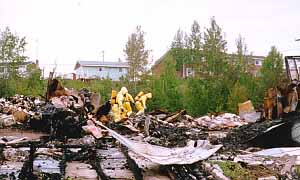 |
The Spill Site
Canning is a small rural community of approximately
750 people located in Kings County in the predominantly
agricultural Annapolis Valley of Nova Scotia. The
village is some 10 kilometers from Kentville, the
site of the County offices designated as headquarters
for the spill response. Main Street closely parallels
the Habitant River which flows 1.5 kilometers to an
abateau (water control structure) at its confluence
with the Minas Basin.
The Maple Leaf Farm Supplies Limited warehouse was
a metal-sided structure on a concrete pad situated
on a hill overlooking Main Street. The pesticides
were stored in a variety of metal, plastic and paper
containers. A large number of propane cylinders and
two of gaseous methyl bromide were also present; the
contents of the latter were not released during the
fire. A nearby retail outlet containing a variety
of farm products was undamaged by the fire. The inventory
records for the warehouse were kept in this building
and were, therefore, not destroyed in the fire.
|
Response, Containment, and Cleanup Activities
The local volunteer fire service responded to the call
at 0200 hours on May 31, 1986; following an assessment of
the situation, the fire chief requested and received mutual
aid assistance from other volunteer departments. He also
contacted Transport Canada's CANUTEC office to obtain information
on potential hazards of products suspected to be involved
in the fire.
Municipal and Kings County officials were promptly advised
and they invoked the County Emergency Response Plan which
fortunately had been thoroughly tested only days before
the fire. By 0300 hours, an evacuation of local residents
by firefighters and the RCM Police was underway. A senior
citizens home was situated very close to the fire site.
Following the evacuation, access to the entire area was
restricted to those involved in responding to the incident.
At 0319 hours, CANUTEC relayed information on the spill
to the Canadian Coast Guard Traffic Centre, who in turn
informed the Nova Scotia Department of Environment (NSDOE)
and Environment Canada (EC), and subsequently other interested
agencies. Representatives of environmental agencies were
on-scene by 0530 hours, May 31, 1986.
Twenty-three firefighters and police officers and one local
resident were treated in hospital for possible exposure
to chemical fumes and then released.
As mentioned previously, in excess of 1.2 million litres
of water was used to control the fire; much later, foam
was also applied; contaminated water left the immediate
site passing over adjacent properties. A trench was dug
to trap water leaving the immediate fire area.
The NS Fire Marshall's officer and the RCMP initiated an
intensive investigation into the cause of the fire since
there had been a number of suspicious fires in the Annapolis
Valley over the preceeding weeks and months. The Fire Marshall
retained control of the site for five days; this did not,
however, impede the monitoring and cleanup activities taking
place there.
Environmental agencies worked closely with the warehouse
owner to develop a detailed and current inventory of products
in the building and with product manufacturers to determine
the safest and most appropriate containment, neutralization
and cleanup procedures.The Fundy Health Unit of the provincial
Health Department placed an immediate restriction on the
use of the municipal water supply until testing confirmed
its safety on June 5th. However, an advisory remained in
effect after this date for five private wells in the area.
The Health Department also coordinated a blood/urine sampling
program (acetylcholinesterase, liver and kidney functions)
for response crews and others potentially exposed to chemicals.
The results of this extensive testing showed no abnormalities.
Milk was collected from local diary herds for pesticide
residue analysis and cattle in the immediate area were given
blood tests and placed under veterinary observation as a
precaution.
On June 3, 1986, NSDOE issued a Ministerial Order requiring
a thorough cleanup of the site by the polluter. The warehouse
owner was unable to fund, on his own, such a large operation.
Following the invocation of the Good Samaritan Act by the
province, the Canadian Agricultural Chemical Association
(now known as the Crop Protection Institute of Canada) agreed
on behalf of the industry to fund the cleanup and ultimate
disposal of contaminated building debris and the remaining
"chemical soup". Environment Canada assisted in
the cleanup efforts by providing a mobile reverse osmosis
unit to treat contaminated water.
Debris was segregated; uncontaminated building materials
were disposed of at the local landfill site while pesticide
residues, contaminated debris and used filters from the
reverse osmosis process were drummed and disposed of at
an approved out-of-the-province hazardous waste facility.
Regular media briefings were conducted throughout the incident
and the media were allowed on site in a controlled manner
for picture taking opportunities. Meetings were held with
affected residents to provide them with detailed information
on the nature of the spilled chemicals, possible health
and environmental implications, and to give them an opportunity
to air any concerns they may have had with respect to the
evacuation, response, and cleanup activities.
The evacuation order for residents in the immediate area
of the fire was not lifted until the evening of June 6,
1986, following an opportunity for those most directly affected
to question environmental and health authorities on their
findings.
Treatment of Contaminated Water and Debris
Manufacturers/suppliers with pesticides present in the
Maple Leaf Farm Supplies Limited warehouse at the time of
the fire (Chipman Chemicals, Union Carbide, Dupont Chemicals,
Velsicol Canada, BASF, Ciba-Geigi and Hoechst Canada Inc.)
responded rapidly to requests for detailed information and
cleanup of their products; they also sent representatives
on site to remove identifiable pesticide products for reprocessing
and disposal. Two cylinders of the fumigant, methyl bromide,
were recovered intact from the site by the supplier. Union
Carbide recovered and shipped 13 drums of waste Temik from
Canning on June 4, 1986.
Following this stage of the cleanup, a hazardous waste
contractor, Sanexen International, was retained to undertake
the warehouse site cleanup. The company deployed a 40 ft.
tractor trailer as an operations centre for the cleanup.
Work crews were outfitted with protective clothing to shield
them from pesticide residues as well as from caustic cleaning
solutions.
The warehouse structure was dismantled and the building
materials along with other large pieces of debris were decontaminated
with a fine spray of detergent and weak caustic solution,
and temporarily stored in a limed and bermed area adjacent
to the fire site.
The company segregated contaminated and uncontaminated
debris; all large uncontaminated and decontaminated building
materials were disposed of in a local landfill. The location
of all items deposited at the landfill site were mapped
for future reference.
Broken containers of chemicals and loose chemicals were
shovelled into labelled steel drums and sealed. The liquid
remaining was contained and either vacuumed into drums or
treated with soda ash and soaked up using absorbent clays.
This material was also drummed and labelled.
Although cleanup crews were able to finally leave Canning
one month after the fire, it was almost a year later in
March, 1987, that the remaining waste on site (50 drums
of manzate waste, 20 drums of waste from the reverse osmosis
unit, 111 drums of waste from the cleanup by Sanexen) was
shipped to Ontario for treatment and disposal at an approved
secure chemical landfill site. This delay resulted from
a shortage of space at the selected disposal site and the
need for the company to obtain approval for, and then develop,
this new storage capacity.
Roughly 100,000 litres of contaminated runoff water and
waste water, generated during site cleanup, collected in
a trench dug down slope from the warehouse. This water was
periodically pumped into a tanker truck to allow settling
of particulates and await treatment and disposal. Removal
of water from the trench also aided decontamination and
dewatering of the fire site. A reverse osmosis unit (mobile
filtering system) belonging to Environment Canada was employed
to process the waste water. The unit consists of a feed
pump, two 5-25 um pre-filters, a high pressure pump and
pressure vessels containing reverse osmosis membranes. This
unit was on scene from June 10 to June 29, 1986. In combination
with activated carbon filters, the unit effectively removed
99 percent of the pesticide residues. Levels in the water
were reduced to below background levels prior to discharge
to the Habitant River. Alum was used to enhance suspended
solids removal prior to filtering. This flocculation step
also tended to significantly reduce the concentration of
some pesticides in the supernatant solution prior to further
processing; for example, atrazine levels declined from 9000
ppb to 200 ppb.
The original volume of waste water noted above was reduced
to roughly 4000 litres of sludge and concentrate, and 400
litres of spent carbon. All of this material was drummed
and disposed of with other contaminants out of province
|